Grimshaw and UEL develop Sugarcrete blocks that "could replace the traditional brick industry"
Architecture studio Grimshaw and the University of East London have collaborated to create Sugarcrete, a biomaterial construction block with an interlocking shape made from the sugarcane by-product bagasse.
Sugarcrete was developed to be a low-cost and low-carbon reusable construction-material alternative to brick and concrete.
The concept, design and fabrication of the material were led by staff and fellows of the University of East London (UEL), including senior architecture lecturer Armor Gutierrez Rivas, Sustainability Research Institute co-director Alan Chandler and research fellow Bamdad Ayati.
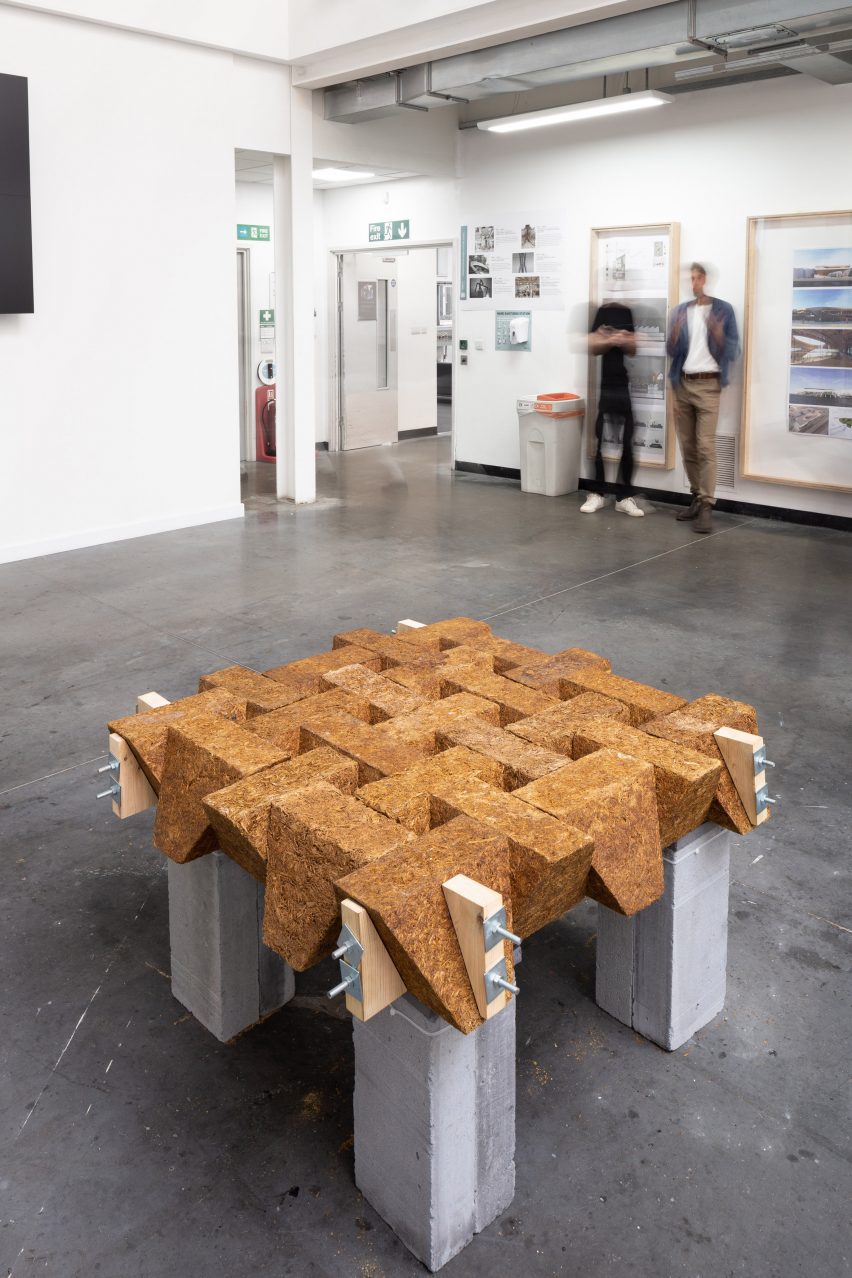
The UEL team developed the material together with Grimshaw architect Elena Shilova and Grimshaw design technology director Andy Watts and with support from sugar brand Tate & Lyle Sugars.
According to the Sugarcrete team, sugarcane is the world's largest crop by production volume, with almost two billion tonnes produced yearly worldwide.
Of this, 600 million tonnes of fibrous bagasse is created as a by-product.
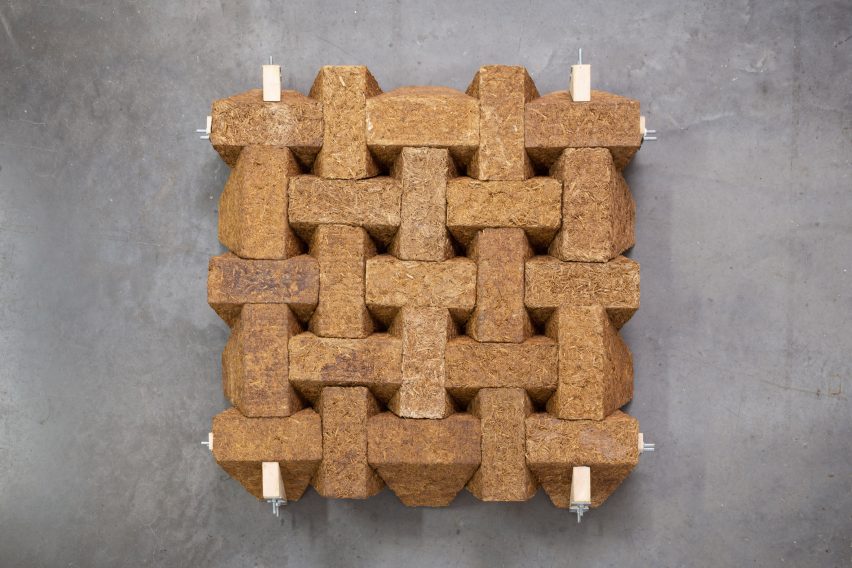
Bagasse was mixed with mineral binders to create the Sugarcrete material, which was designed to be four times lighter and have 15 to 20 per cent of the carbon footprint of traditional bricks.
The material is also cheaper than concrete and its carbon emissions are 20 times lower, according to the team of researchers.
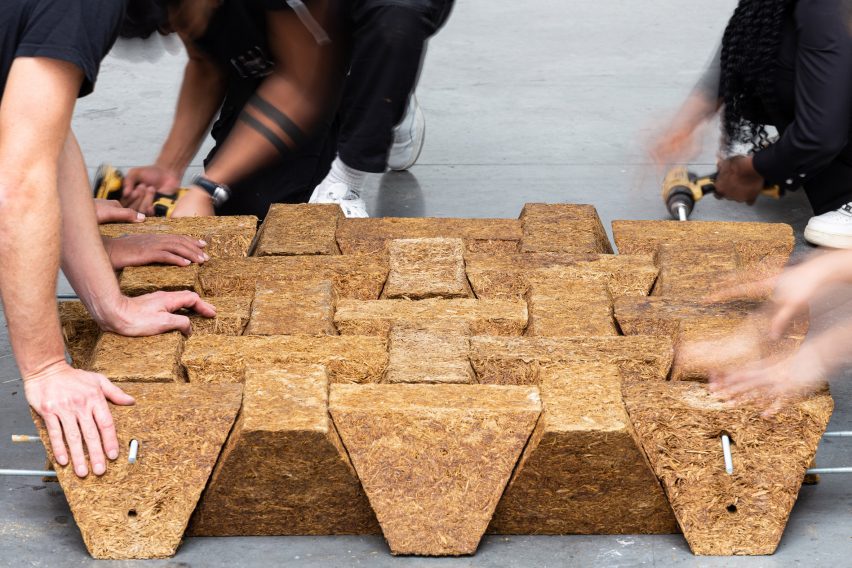
"Using only 30 per cent of the world bagasse production, Sugarcrete could replace the traditional brick industry entirely, offering a potential saving of 1.08 billion tonnes of CO2, three per cent of the global CO2 production," said the Sugarcrete team.
"What we build with, how it locks in carbon and, critically, who benefits in its production and deployment are fundamental to the research plan of Sugarcrete."
Architects at Grimshaw developed a polyhedral shape with tapered sides that was used to form the material into interlocking blocks, informed by French engineer John Abeille's 1699 design for flat-vaulted roofing.
The interlocking modules were arranged in alternating orientations and held together by post-tensioned perimeter ties to create the Sugarcrete Slab, a modular floor slab that can span up to three metres without the need for mortar.
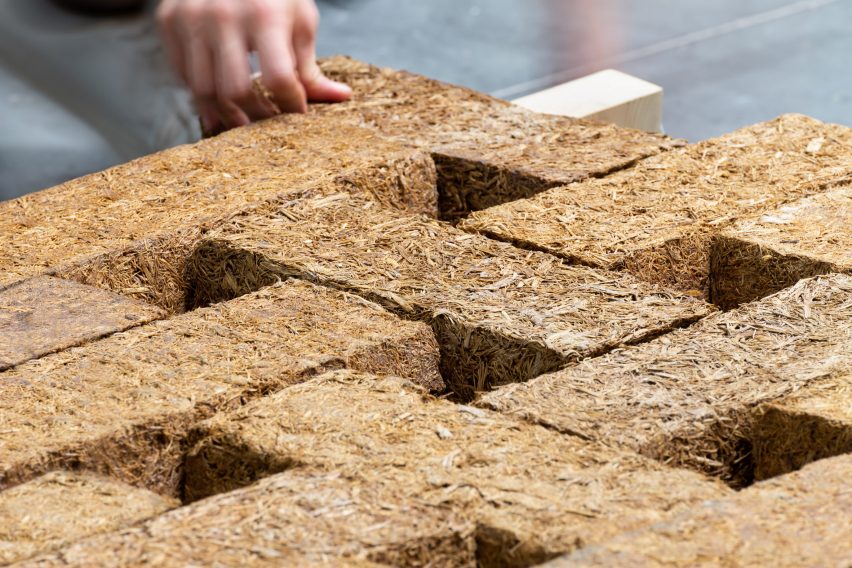
Using robotic fabrication and augmented reality (AR) technology, the blocks were designed to be easily constructed and disassembled so they could be reused for multiple projects.
The Sugarcrete material also has insulating properties and is fire-resistant. The project team suggested the material could be used for insulation panels, load-bearing walls, and structural floor and roof slabs.
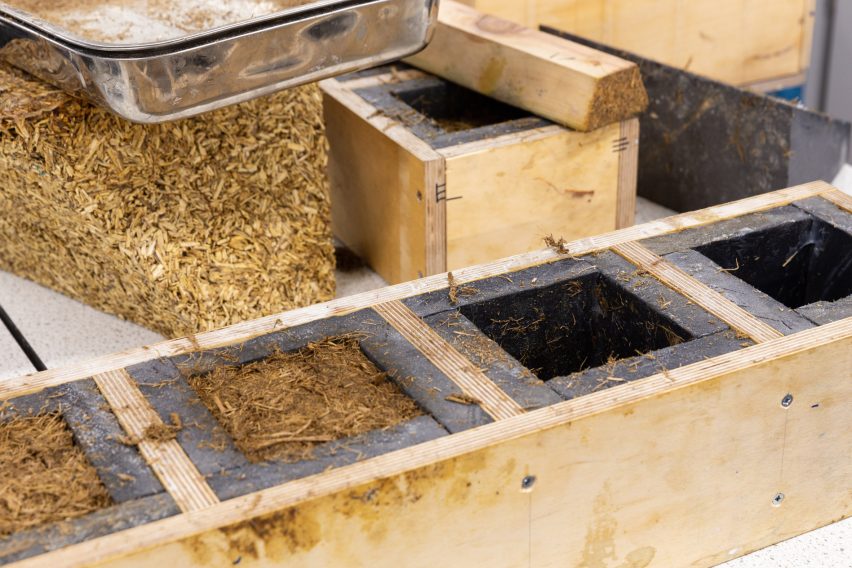
"Challenging misconceptions of waste-based materials being inferior in structural strength, Sugarcrete can offer self-supporting structural applications beyond infill," said the Sugarcrete team.
"Grimshaw's interest in interlocking geometries has brought new opportunities to deploy Sugarcrete as a spanning element to construct a demountable, reusable, fire-resistant composite floor slab called Sugarcrete Slab," it continued.
"Due to reciprocity and distributed forces network, the system performs superior to the conventional monolithic assembly."
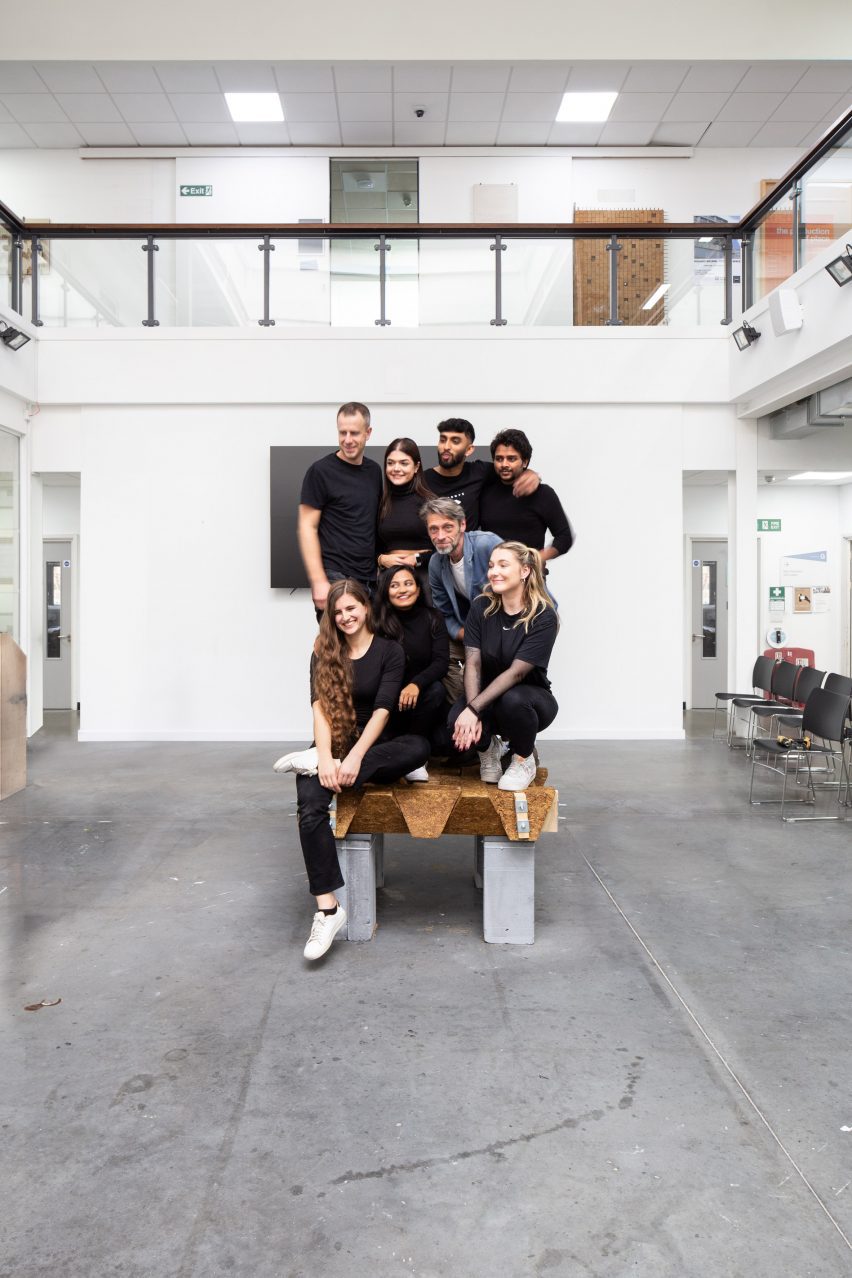
The research behind Sugarcrete is publically accessible with the hope that the material will be produced worldwide, particularly in communities where sugarcane is locally grown.
Nominated for the 2023 Earthshot Prize, the project team plans to further develop the Sugarcrete material, which UEL has trademarked.
"Future structural tests will be focused on studying the shear and tensile capacity of the material, which can then be used to experiment with and possibly reduce the distribution of reinforcement within the system or increase the span capacity," the team told Dezeen.
"The design team is exploring how to deploy the material in live projects working within the local context of sugarcane harvesting communities in the global south," it added.
"The next steps of the research will see the development and co-design of digital tools linked to by-product availability from diverse crops and regions and performance criteria that maps the potential to deploy Sugarcrete globally."
Other construction materials made from waste or biomaterials include a low-carbon brick made from local municipal waste and a concrete-alternative bio-brick made from charcoal and loofah.
The photography is by Chromaphotography and the video is by Jude Adoasi.