Arup unveils its first 3D-printed structural steel building components
News: engineering firm Arup has produced prototype 3D-printed steel construction joints that could be used to create more efficient structures.
Arup says it has produced a new design method for creating "critical structural steel elements" for tensile structures – a development it believes signals "a whole new direction for the use of additive manufacturing in the field of construction and engineering".
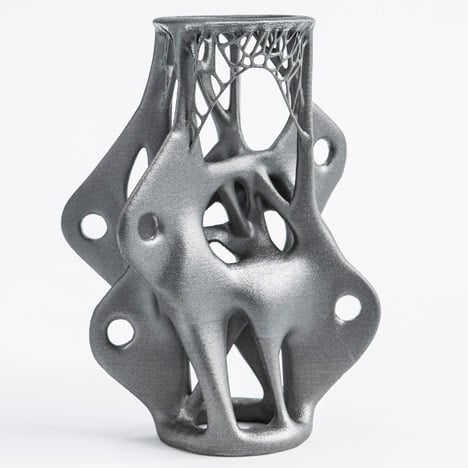
The technique will allow the company to produce bespoke structural pieces more efficiently, and is expected to significantly cut waste and costs.
"Most importantly, this approach potentially enables a very sophisticated design, without the need to simplify the design in a later stage to lower costs," said Salomé Galjaard, senior designer and project leader at Arup.
Made from maraging steel, each of the 14-centimetre-tall prototypes is produced at just under half the size of a real node and has been put through preliminary material tests.
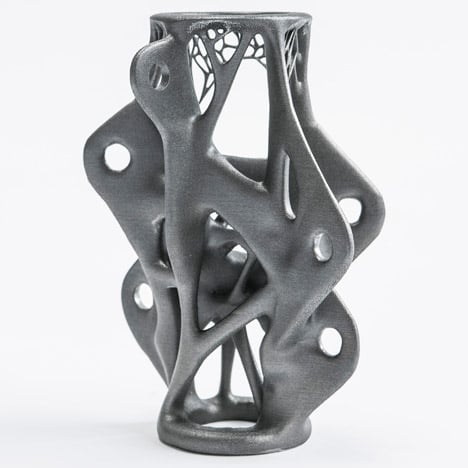
Galjaard told Dezeen that the firm hoped to use the technique to produce elements for full-scale projects within a year.
"We were actually quite surprised to see no one in the building industry was applying this technique so we thought why don't we give it a shot and try to design something with a very open mind," said Galjaard.
"What you see here is a nice model but it's definitely not the most optimised version. We're going through the design process again, trying to get rid of all those traditional thoughts that were still in our heads. We actually think that the next node will even look different than the one you see in the pictures."
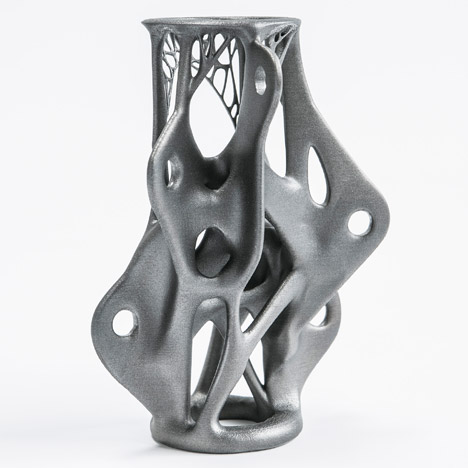
Arup worked with specialists at CDRM, the UK-based 3D-printing agency bought by rapid manufacturing giant 3D Systems last year, as well as engineering software and consultancy company WithinLab and 3D manufacturing developer EOS.
Galjaard said that the nodes had originally been designed to be produced in stainless steel, but maraging steel was easier to print.
"CDRM had a machine that was printing maraging steel and it was easier for them to print in this particular steel, which is actually very strong – it's four times as strong as normal construction steel."
"Now, going through the design process again, we're also taking more advantage of the strength of this material and that's also why we expect the next edition of the nodes will be much slimmer and smaller and lighter."
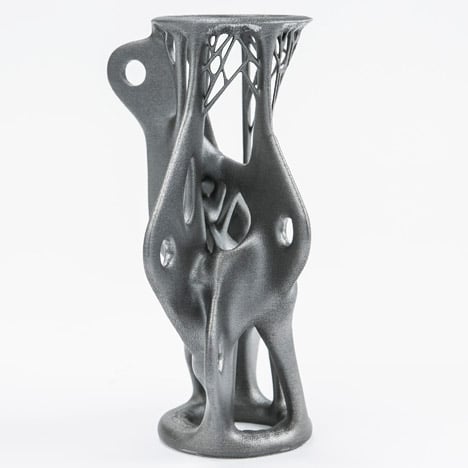
Printers are not currently available at a big enough size to produce other, larger construction elements, said Galjaard.
"What is important to realise is that the industry didn't have any requests before for large printed products [of this nature]. No one else has come to them before. So the size of the products, yes it is limited, but bigger machines are being developed."
"Most of the materials available now are also developed for a specific purpose or maybe even a specific client. So I can imagine that could also happen for the building industry as long as we let them know what kind of characteristics we require, it can be adapted to our needs."
Product designers have already been experimenting with 3D printed metals. Dutch designer Joris Laarman recently showed a three and a half metre long, two metre wide printed steel mesh bench as part of a gallery exhibition in New York.
Here's an edited transcript of our interview with Salomé Galjaard:
Anna Winston: Could you tell me how the project came about?
Salomé Galjaard: We were working on one of our external projects with my colleagues in Amsterdam, which was a large tensegrity structure for a shopping street in the Netherlands that would contain lighting, street lighting project, but those structures were tensegrity structures.
Anna Winston: What do you mean by tensegrity?
Salomé Galjaard: Tensegrity is a type of structure which consists of struts and cables that are connected, and by putting tension on the cables, the cables provide tension and the struts provide compression, and it is in perfect equilibrium. It's a very specific type of structure, it's not something that's normally used in standard buildings. We used it in Australia and we were using a similar type of structure for this street lighting project in the Hague in the Netherlands.
We worked on it for a quite a long time and because we made the shape of those tensegs irregular, we ended up with all the nodes that were connecting the cables in the struts, being all slightly different. And we actually spent quite a long time trying to figure out if we could come up with a better solution than 1,200 different nodes. One solution, or maybe a couple of families of solutions, we didn't really manage on that particular project.
So the project was finished with the client and the contractor but it was nagging a bit, it wasn't really a satisfying solution. So we thought "why don't we try to find a better solution as an internal resource project?" For that we started looking at 3D printing. We started about one and a half years ago. We were trying to learn about the machines that were available and the materials that were available and also looking at other industries, at what they were doing.
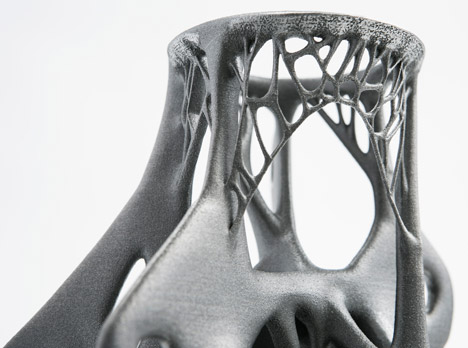
We were actually quite surprised to see no one in the building industry was applying this technique so we thought "why don't we give it a shot and try to design something with a very open mind, with the idea that it could easily fail or not be something that we would want to use?" We went through the design process and ended up with what you see in the pictures. We were actually quite positively surprised and during the process learned more about how production was done – how you could design from production, what the material characteristics were. We did some very simple material tests ourself and thought even those were actually quite promising. I would like to stress that was not full-scale material testing, especially in that topic there is a lot to be done. But we were pleasantly surprised.
On the other hand, we also realised especially during production that we were still very limited by traditional thoughts. We thought we gave ourselves all the design freedom we could, using this technique to its best advantage, but during the process we realised we were still using traditional thinking. Traditional designing to using traditional production techniques. What you see here is a nice model but it's definitely not the most optimised version. We're going through the design process again trying to get rid of all those traditional thoughts that were still in our heads. We actually think that the next node will even look different than the one you see in the pictures.
Anna Winston: So what exactly are you printing with?
Salomé Galjaard: We worked together for the printing with 3D Systems – they do a lot of printing in metal already, but just for other industries. For healthcare and dentistry and also for I think the aviation industry. They explained more about the design rules for production because we realised it's one thing to design for function, but this production also has requirements as well. You can print almost anything, but if you want to do that in a smart and financially interesting way there are rules to take into account. So we figured out what those were and adapted our functional model to that. Then we printed this model which you see in the pictures which is actually scaled down for cost reasons, but also because the machines are still relatively small.
The nodes are scaled to 40 per cent of the original size. We could have printed them in almost real size but because for us it was just a model, we didn't print a full-scale model because it was getting a little bit expensive for an internal research project. We could have printed them bigger, but at the moment in the picture they are about 14 centimetres high.
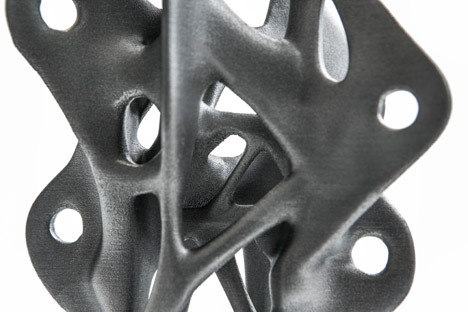
Anna Winston: So you haven't used them practically yet?
Salomé Galjaard: No, this one node that you see that is the result of the first part of our research. We did some simple material testing in the university and those results – but again this is only a small part of the material testing that we are officially doing – we're matching exactly with the material specs that we got with the EOS, because it was printed on an EOS machine. They also advised us to use a material that is approved to be used on that machine, that comes with a material specification that lists material characteristics. We were quite surprised to see that our simple tests were actually very, very similar to the characteristics listed in that material spec.
Anna Winston: Is printer size a significant limitation?
Salomé Galjaard: Yes, absolutely. The printer has a building chamber which is at the moment a certain size. I have been told that the main innovations are working towards bigger machines. What is important to realise is that the industry didn't have any requests before for large printed products [of this nature]. No one else has come to them before. So the size of the products, yes it is limited, but bigger machines are being developed. But also, for example, the materials. Most of the materials available now are also developed for a specific purpose or maybe even a specific client. So I can imagine that could also happen for the building industry as long as we let them know what kind of characteristics we require, it can be adapted to our needs.
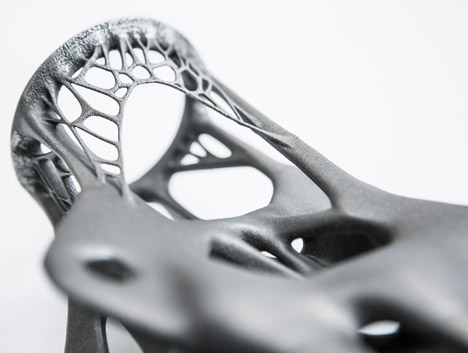
Anna Winston: The material that you're using for this prototype, what is that exactly?
Salomé Galjaard: This material is called maraging steel. Actually, the node that we designed was not designed for this material, it was designed for stainless steel. CDRM had a machine that was printing maraging steel and it was easier for them to print in this particular steel which is actually very strong – it's four times as strong as normal construction steel. Now, going through the design process again, we're also taking more advantage of the strength of this material and that's also why we expect the next edition of the nodes will be much slimmer and smaller and lighter.
Anna Winston: Do you see this being something that will actually be cost effective in the long run? Right now it's quite an expensive thing to do.
Salomé Galjaard: We did make an estimate. I think what's very important is to take the whole lifespan into account – everything from designing to producing and building and recycling. If you just isolate production it's going stay expensive. Especially machine time, which I'm told is the most expensive part: it's not necessarily the material itself, it's the time it spends in the machine. Since building elements are relatively large, it can be a pricey thing to do. On the other hand, if you realise that you can make a product that is much lighter and if you have many elements of that in a structure, the structure as a whole could become lighter. That has a positive influence not only on the printed part but also on other elements in the building. Things like storage and transport should also be taken into account. So this is something that can be produced relatively shortly before installation if there's weight reduction and if the elements are small then transport can be more cost effective and cheaper.
A lot of people are talking about weight reduction, which is logical, but what's really interesting to me is that print functions can be much more easily integrated into one product. And that I think has a very positive influence on installation costs. So if you look at all those different elements, then I do think for some projects it can be cost effective. But it also very much depends on how the products are designed and produced.
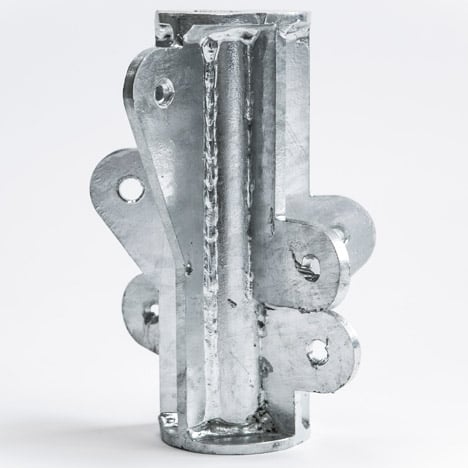
Anna Winston: How long do you think it will be until you've got something you can actually use on a project?
Salomé Galjaard: What's very difficult for the engineers here in Arup is that they don't really know what to expect, they don't have a gut feeling with this material and this production technique and they do have that will all the other standard products that we use. Before we start applying it in large scale buildings, I think we need to gain a lot more experience. But I think we can do that with smaller projects that are less critical maybe to people in and around it.
Anna Winston: Are we looking at this year?
Salomé Galjaard: Yes, I hope if we find the right part and the right project I hope to start doing that before the end of the year. I can imagine it can be quite difficult to find the right project because this kind of manufacturing shouldn't be the goal. You should build something in the most cost-effective or the best way to come up with the best end product. I think this is only for very specific projects. We're trying to figure out now what those projects might be.