3D-printed bridge "combines ancient wisdoms and modern technology"
The Striatus bridge makes use of historic masonry construction techniques and modern technology explains Zaha Hadid Architects associate director Shajay Bhooshan in this instalment of Dezeen's Concrete Icons video series produced in collaboration with Holcim.
The video features Striatus, a freestanding 3D-printed concrete footbridge designed to demonstrate how 3D printing techniques can be used to build with less material.
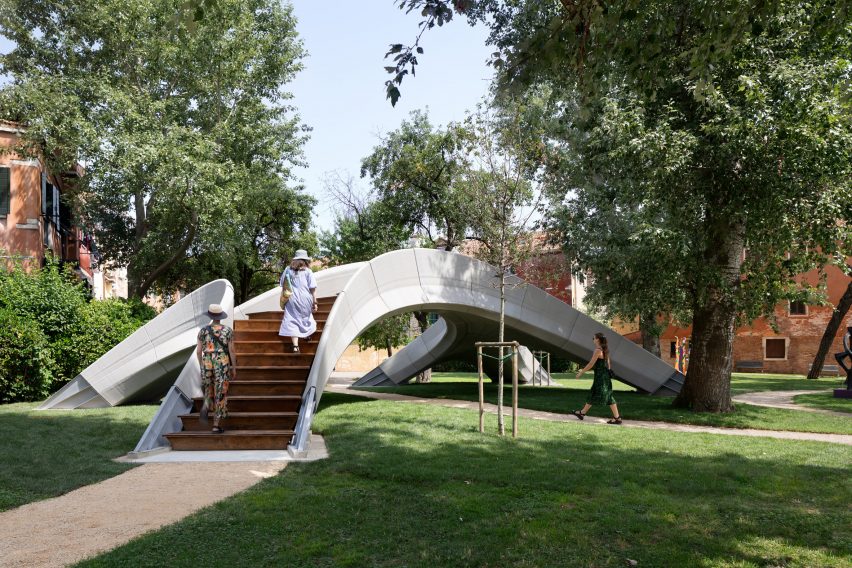
Speaking to Dezeen in an exclusive video interview filmed at Zaha Hadid Architects' office in London, Bhooshan explained how the bridge was built to showcase the capabilities of unreinforced concrete and computational design.
"Striatus demonstrates that combining ancient wisdoms of masonry construction, modern technologies of design and engineering and 3D concrete printing, we can achieve a pathway to sustainable use of concrete," he said.

The arched bridge was constructed from 53 hollow blocks, each printed from 500 layers of concrete ink, which took 84 hours to print.
The Striatus bridge was printed using a six-axis robotic arm that can print non-uniform, non-parallel layers, which allowed for the printing of arched components that can be used structurally.

The bridge makes use of historic masonry construction techniques to enable the load of the structure to be distributed without the need for internal ancillary support, which means it is held together entirely through compression.
"Striatus is assembled the same way as other ancient masonry construction, which fully engages the compression capacities by thinking of concrete as an artificial stone," Bhooshan said.

The bridge is dry assembled without any glues, binders or mortar, which means it can be more easily disassembled and recycled. Instead, it uses neoprene pads to control friction and stress concentration, as well as external ties to absorb thrust tension.
The lack of adhesives and mortar mean the bridge has a lower environmental footprint and improves its circularity.
"The masonry principles also help it to be extremely recyclable, because it is dry assembled, and there is no steel to be separated out," Bhooshan said. "It can be dismantled and crushed and cleanly reused."

Since the blocks used to make the bridge are hollow, considerably less material was used.
"The concrete ink is deposited layer by layer," he explained.
"You can place material only where it's needed a bit like our bones, which are hollow – there's only material where there's forces flowing through it."

Striatus was originally conceived for and installed in the Giardini in Venice, as part of the Venice Biennale in 2021.
It was built by Block Research Group at Swiss university ETH Zurich and the Computation and Design Group at Zaha Hadid Architects (ZHA CODE), in collaboration with concrete 3D printing specialists incremental3D.

Concrete Icons is a six-part video series created in partnership with building materials company Holcim, which profiles the most striking contemporary concrete buildings by the world's leading architects.
Previous instalments in the series focus on MAD's sinuous Cloudscape library in Haikou, China and The Broad museum by Diller Scofidio + Renfro.
Last week's instalment focussed on The Square, a learning centre comprised of stepping cubic volumes by Japanese architect Sou Fujimoto.
The photography is by Naaro unless stated otherwise.
Partnership content
Concrete Icons is produced by Dezeen for Holcim as part of a partnership. Find out more about Dezeen's partnership content here.
Build the icons of the future with Holcim's low-carbon ECOPact concrete, delivering up to 90 per cent less carbon dioxide emissions compared to standard concrete with no compromise on performance.
Find out more about how Holcim works with architects here.