Six examples of fabric-cast concrete that are breaking the mould
Pouring concrete into fabric moulds allows designers to create dramatic, sculptural shapes that could soon be used for architectural structures. We've selected six of the most interesting examples, including a new casting technique using robots.
The fabric casting of concrete involves pouring cement into a textile mould, usually held in shape by a wooden frame.
The technique was pioneered by the likes of the University of Manitoba's Centre for Architectural Structures and Technology (CAST) and 20th century Swiss engineer Heinz Isler, who used it as part of his work developing super-thin concrete building shells.
But recently, designers have been experimenting with it again to create unique sculptural furniture as well as exploring its potential for creating new kinds of architectural components, introducing robots and different fabrics into the casting process.
According to engineering and architecture firm Atkins, fabric casting could allow architects to create interesting structures with up to 40 per cent less concrete, and may also mean that buildings could be made with less labour.
"This casting method has implications at various scales in the construction site of the future," said designer Joseph Sarafian, who has been working on a way to make the casting process more efficient using robots. "We see it being scaled up to create unique building facade elements or even the primary structure of a building."
Here are some stand-out examples of the technique we've seen at Dezeen:
Fabric Forms by Ron Culver and Joseph Sarafian
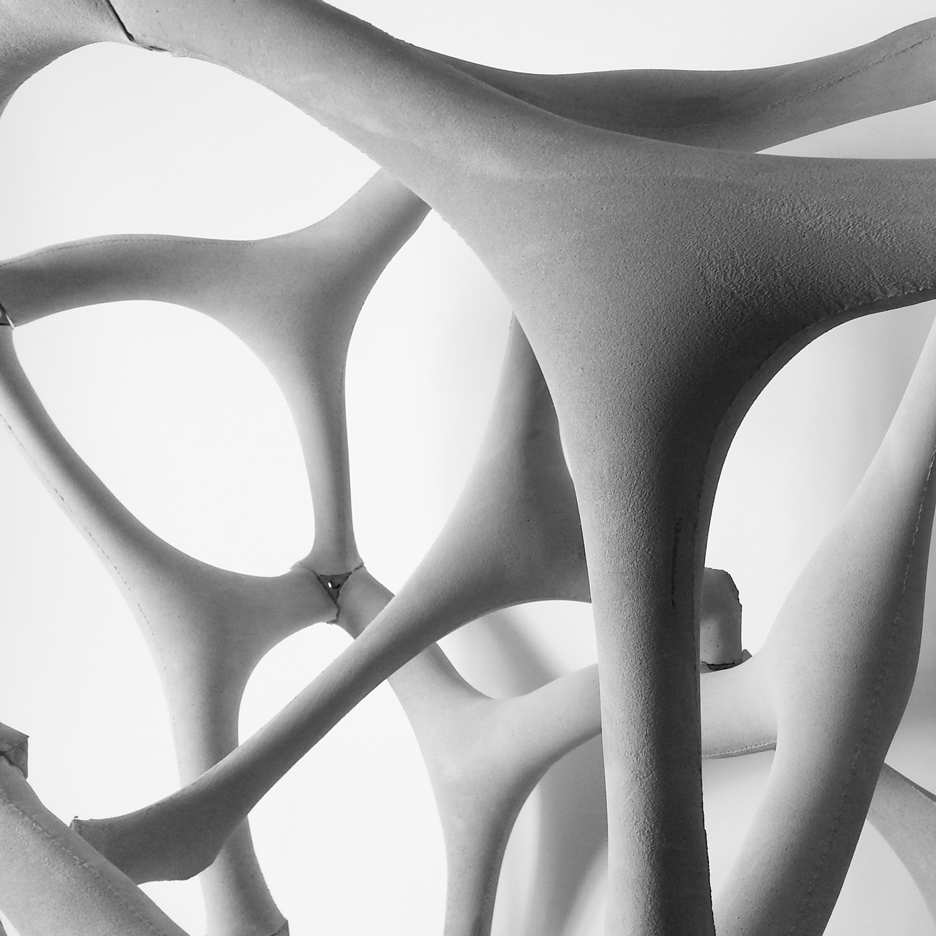
Designers Ron Culver and Joseph Sarafian progressed concrete casting techniques by adding robots. Carried out at the University of California, the Fabric Forms project involved pouring a concrete and fibreglass mixture into Y-shaped Lycra sleeves stretched into position by six-axis robots.
By using robots, the designers do not have to constantly create and destroy the plywood framework that is usually built to hold a fabric mould in place. They told Dezeen this could be the construction technique of the future.
"Parametric design is increasing the need for variation, much of which goes unbuilt because of traditional construction methods' failure to adapt to new digital technologies," Sarafian told Dezeen.
"We see Fabric Forms as one of many ways to bridge that gap." Read more about Fabric Forms »
Augmented Skin by students from the Bartlett School of Architecture
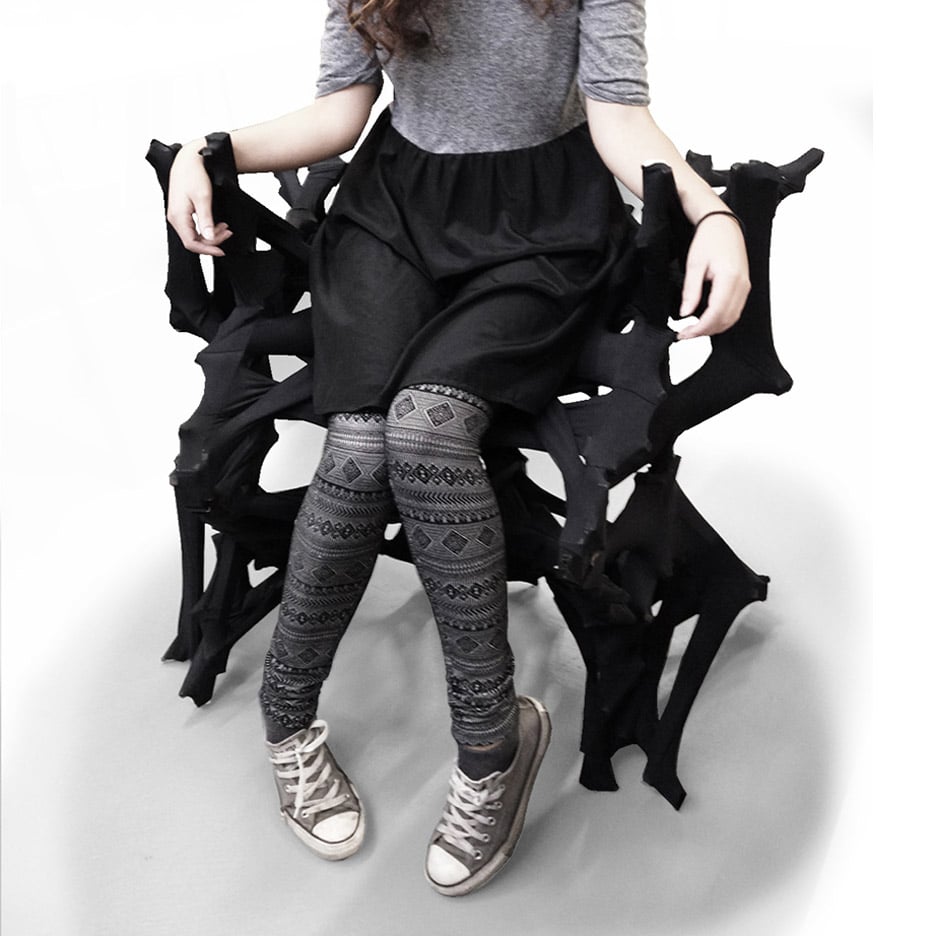
Graduates from London's Bartlett School of Architecture developed an experimental technique for creating intricate building components by using sticks wrapped in stretchy fabric to cast concrete.
Once the sticks have been positioned inside the fabric to form joints, concrete is poured in to create a solid connecting form without the need for a supporting framework. The sticks remain inside the mould, reinforcing the structure.
Called Augmented Skin, the projected involved creating a few small prototype objects, like a chair, using the technique. The students also developed several visualisations of the sorts of architectural structures that could one day be created, including pavilions and bridges. Read more about Augmented Skin »
Papabubble at Tokyo Daimaru by Schemata Architecture Office
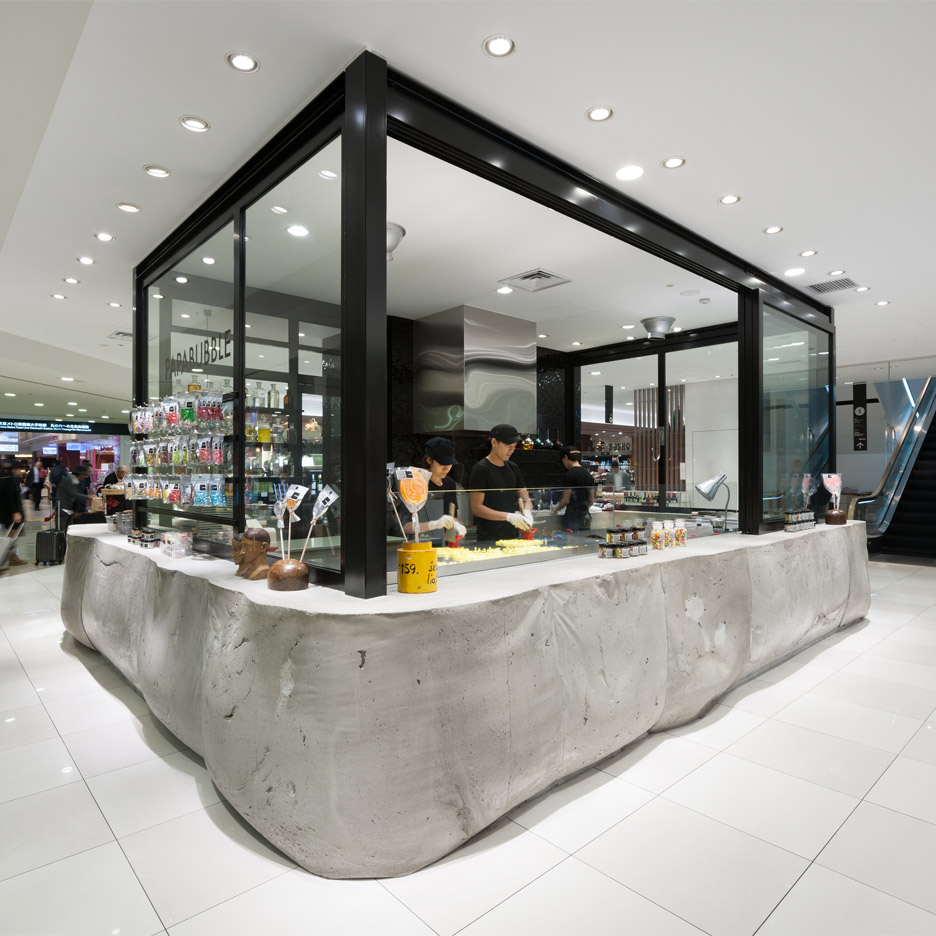
Most of the recent experimentation with fabric-cast concrete has created intricate web-like forms. But Japanese studio Schemata Architecture Office cast concrete in a fabric bag to create this chunky counter for a confectionary kiosk in Tokyo.
The concrete counter folds around the kiosk and displays the rounded edges and creases of its fabric mould. "We made the concrete with an uncommon method, but it was not easy," Nagasaka told Dezeen. "The concrete pressure is very heavy, but we found a hard enough textile finally." Read more about Papabubble »
Mass IIII by Janwillem Van Maele
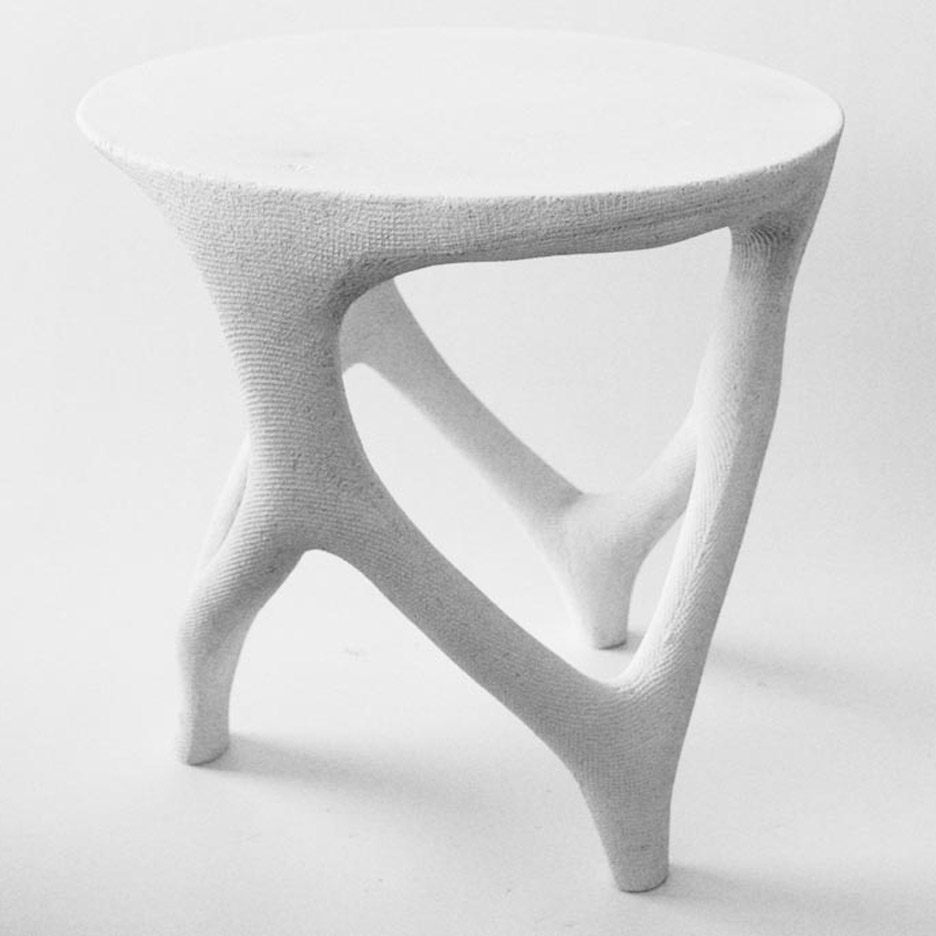
De Hogeschool West-Vaanderen graduate Janwillem Van Maele cast this concrete side table inside a suspended fabric mould.
Called Mass IIII, the table was created by stitching the fabric into a net and stapling it to a circular board. This was hung upside-down and filled with cement and gravel, weighted, then drenched in water and left to harden.
The resulting shape was sanded back before cork feet were added to make a functional side table or stool. Read more about Mass IIII »
FattyShell (v.01) by Kyle Sturgeon, Chris Holzwart and Kelly Raczkowski
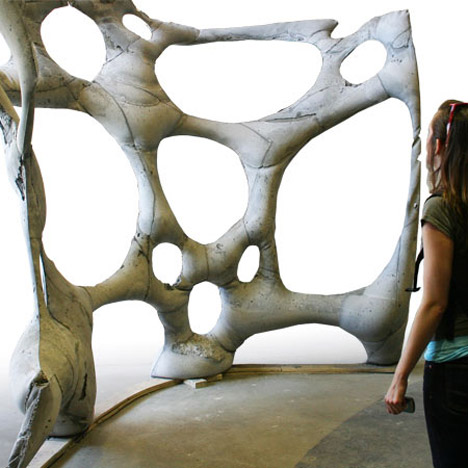
A team of students from the University of Michigan created FattyShell (v.01) as part of their studies into digital fabrication and algorithmic design.
They stitched together sheets of rubber to create a membrane, which was supported by plywood discs to help control the shape of the concrete once poured in. The rubber casing was also tensioned at certain parts with cables.
The cement-based concrete was then poured between the sheets at three hourly intervals. Read more about FattyShell (v.01) »
Stitching Concrete by Florian Schmid
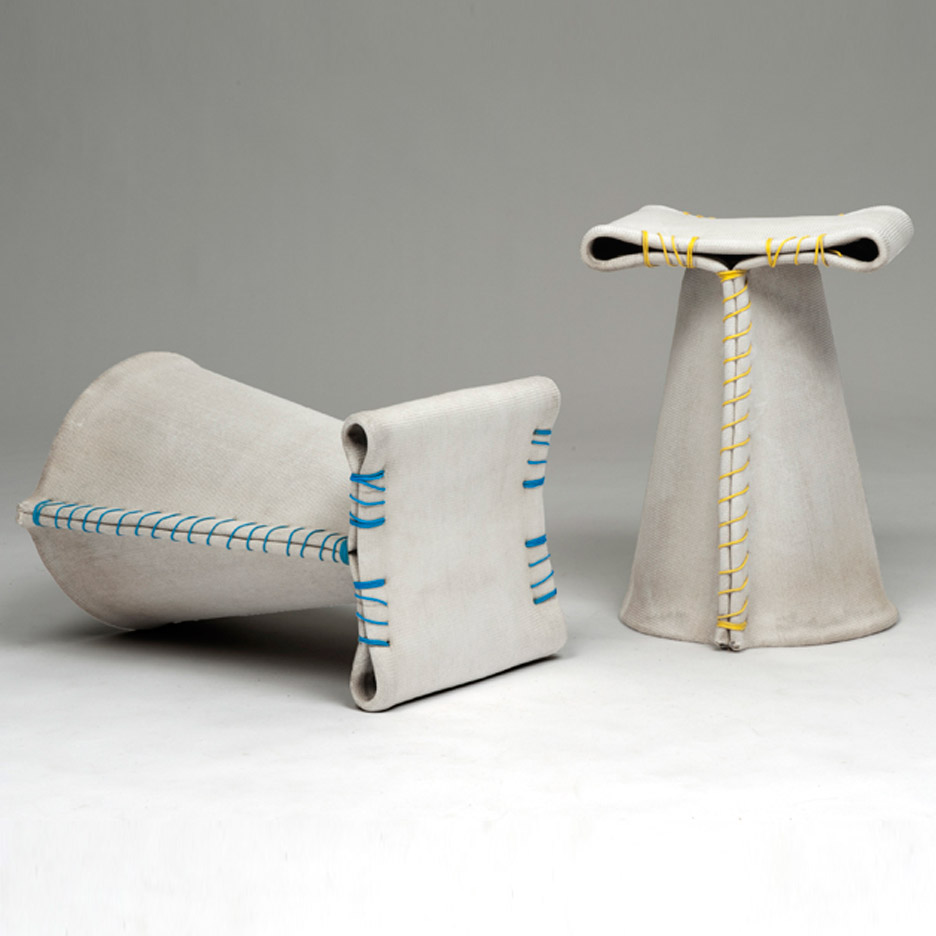
An alternative to casting concrete in fabric is to use fabric that is actually impregnated with concrete. This achieves a different aesthetic and has not yet been used to create load-bearing building structures.
Industrial design graduate Florian Schmid made these stools from a material called Concrete Canvas, which consists of cement layered between fabric and a PVC backing. Once soaked it can be manipulated for a few hours before hardening.
Schmid folded pieces of the canvas and stitched the edges together with brightly coloured thread, then supported it on a wooden mould while it was drenched in water and allowed to harden. Read more about Stitching Concrete »