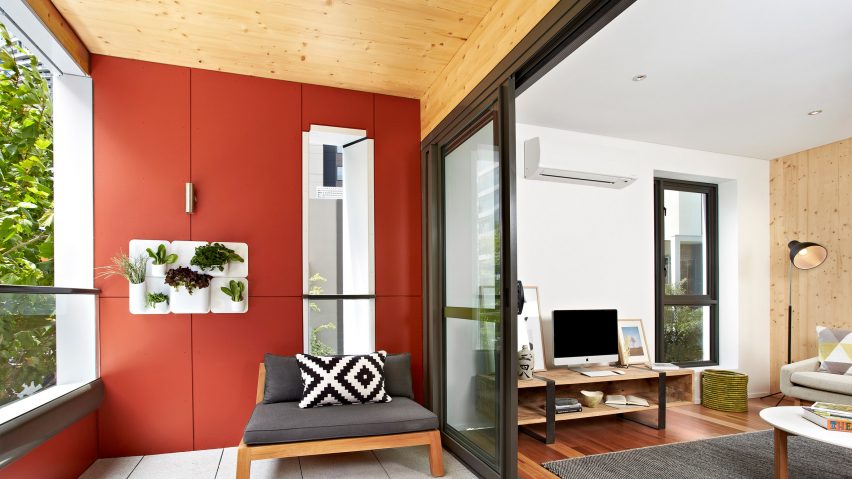
Lendlease's mass-timber tower was shipped from Austria to Australia
As we continue our Timber Revolution series, we look at Australia's first mass-timber high-rise apartment building, which was built from cross-laminated timber grown in Austria.
Built in 2012, the 10-storey Forté block was the world's tallest timber residential building – measuring 32 metres tall – when it was completed.
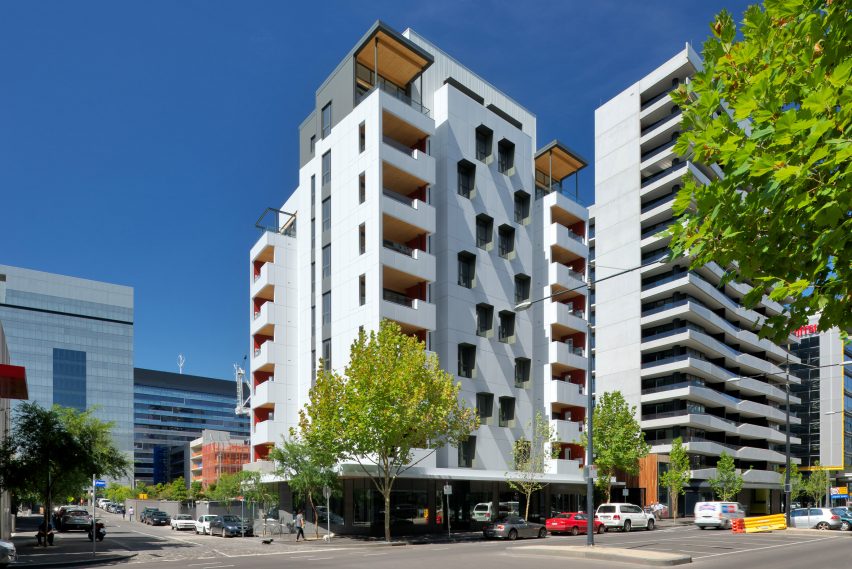
The building was made from 759 cross-laminated timber (CLT) panels created from European spruce, which was grown and harvested in Austria by manufacturing company KLH.
Once harvested, the timber was processed into CLT at KHL's Austrian factory, before being flat pack-style shipped to Australia.
"A showpiece for natural and new"
It was designed to showcase the potential of using CLT in Australia, despite the material not being available locally.
"A showpiece for natural and new, it is where modern architecture meets a natural building material, called cross-laminated timber (CLT), which will unlock a new era in the future of sustainable development and healthier living," said Lendlease at the time of completion.
"Unlike Europe where the revolutionary material has been used for more than a decade, Australia is only at the beginning of its CLT journey and still has a way to go to recognise the enormous potential in our market."
Located in Melbourne's Victoria Harbour, Forté consists of 23 residential apartments with three apartments per floor and retail amenities located on the ground floor.
The building is cubic in form and features a multi-faceted exterior that is punctuated by protruding windows and timber-lined balconies, which extend up the four corners of the building. It was wrapped in a rain screen that protects the timber from the elements.

Its apartments were designed to maximise sunlight and ventilation potential. The CLT flooring of the building's structure was extended to form balconies at each apartment. The undersides of each balcony were left exposed, yet sealed with a polyurethane seal, to reveal hints at the building's CLT construction.
Bathrooms were designed as pods, meaning they were completely prefabricated and installed into apartments as modular components.
Forté "lower impact" despite timber transportation
The building was the second apartment block in Australia to achieve a 5 Star Green Star rating from the Green Building Council of Australia.
Although the building's foundations were constructed from reinforced concrete and its ground and first-floor slabs using geopolymer concrete, the largely timber structure reportedly had a 22 per cent lower carbon footprint than comparable structures.
"Forté reduced CO2 equivalent emissions by more than 1,600 tonnes when compared to concrete and steel – the equivalent of removing over 400 cars from our roads," said Lendlease.
Even with the timber imported from Europe, the structure still maintained a lower negative environmental impact than similar buildings that were constructed using concrete concluded a report completed by RMIT University in 2013.
"Even though the CLT is imported (whereas the reference building's materials are mostly locally produced), the Forté building still has a lower impact for materials and transport combined when compared to the reference building (which utilises concrete)," it said.
"We had to battle against a headwind"
At the time Lendlease's former head of sustainability for Australian businesses Cate Harris explained that Forté aimed to "unlock a new era in the future of sustainable development by making a significant reduction in its embodied carbon impact".
"CLT is revolutionising the use of timber in construction by introducing a more efficient and environmentally-friendly construction process that has not been undertaken in Australia before, but has a proven track-record through Europe," she told The Fifth Estate in an interview.
"CLT is another example of how we are leading the way with innovations that will challenge and improve current building practises in the industry."
Being Australia's first CLT apartment building, the structure had to demonstrate both the viability and safety of the material.
"We had to battle against a headwind just about all the way through process," said Lendlease's Andrew Neiland.
"But by always keeping in close contact with the authorities, banks, insurance companies and other stakeholders, it all worked out. The building was eventually approved on every level, and all the apartments were sold and the shops rented out."
Following the building's completion, regulations were changed to allow mass-timber structures to be constructed easier. At the time timber buildings in Australia were restricted by the National Construction Code's Building Code of Australia, which required intensive review processes for CLT buildings over three storeys.
Australia's building regulation codes changed after Forté
To comply with the building regulations, Lendlease worked with fire safety and risk engineering specialists Scientific Fire Services to engineer an alternative solution to demonstrate the building's fire safety performance and recognised it as a deemed-to-satisfy solution.
"By understanding current CLT research and technology coupled with the application of fire safety engineering methodologies for the Forté building, our engineers successfully delivered this truly groundbreaking project,'' said Scientific Fire Services director Russell Kilmartin in a report.
In 2016, Australia's building regulation codes were changed to allow the construction of timber-framed structures up to eight storeys tall without the requirement of lengthy review processes.
"CLT will transform the construction industry by introducing a more efficient and environmentally-friendly construction process that has never been undertaken in Australia before," said Mark Menhinnitt, Lendlease's former Australian business CEO in 2012.
"With an increasing number of people moving to urban areas, this innovation is timely given the urgency to create liveable, sustainable cities that are climate positive," said Menhinnitt. "The adoption of green technologies, materials and construction processes, like CLT, means we are closer to achieving this."

Timber Revolution
This article is part of Dezeen's Timber Revolution series, which explores the potential of mass timber and asks whether going back to wood as our primary construction material can lead the world to a more sustainable future.